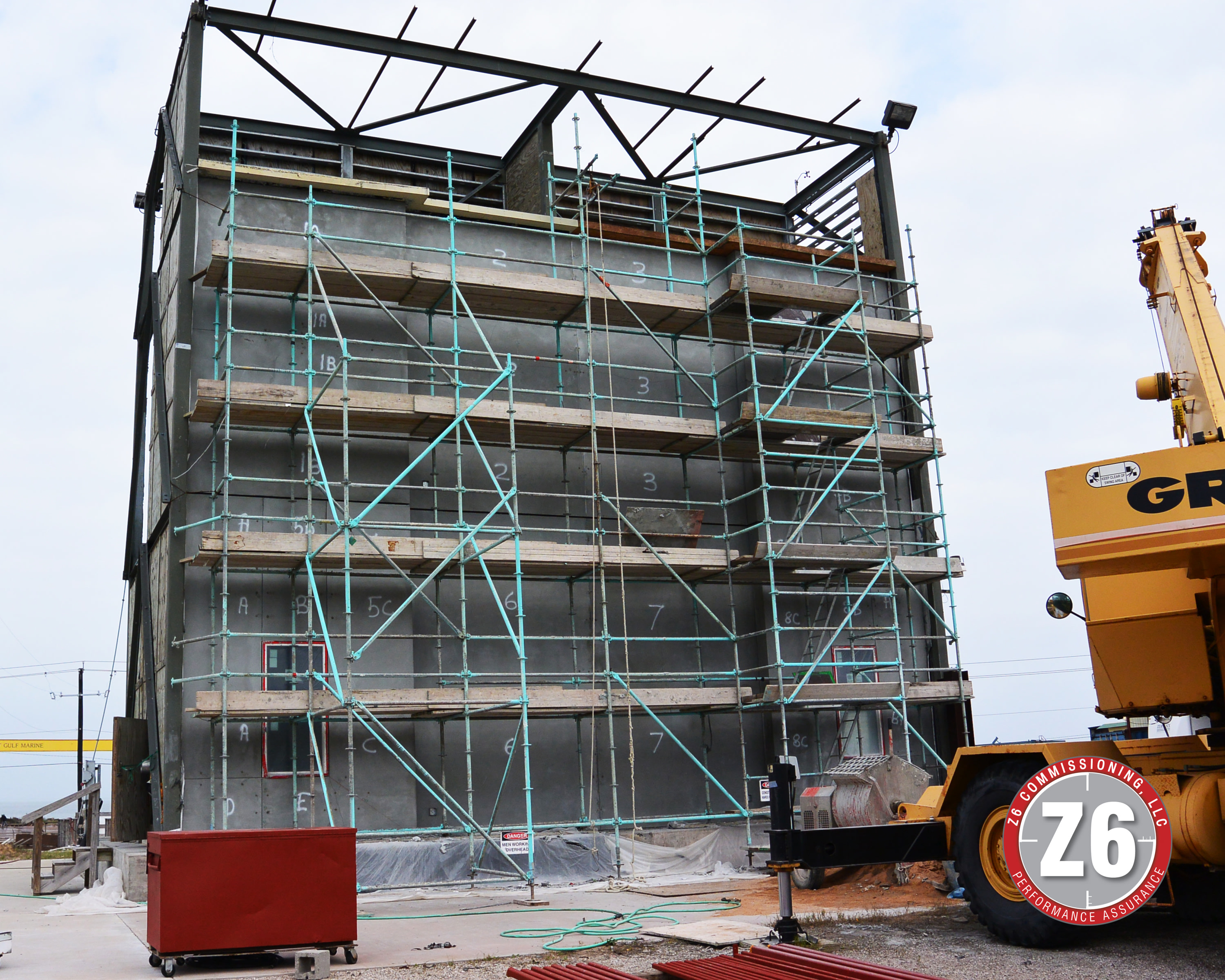
Call me Sasquatch
Rant #2025-03-20
Way back when, when I was a little dude, I wanted to be an architect. In fact, my dad (Pop) wanted me to be an architect; it was one of those things we agreed on. Pop was a general contractor who started as a carpenter at a very young age, progressed to be a foreman, then a superintendent, then an estimator, and finally ended up buying the company. To say that he understood all aspects of the construction process would be an understatement; he was well-rounded in his art (I thought his path was the normal path to being a contractor.) His desire for me to be an architect was largely based on his desire for me NOT to be a contractor. Bonding and banking were rough on contractors in the 70’s and 80’s and he wanted me to have it better. He knew I was “into construction” and that there was no way to derail that train, but maybe he could influence me towards a less brutal part of the industry. I was a creative kid with a technical edge, so architecture seemed natural. That said, I pursued architecture in the same manner that Pop pursued construction. That is, starting at the bottom and working your way through the entire process (design, CD’s, specs, PM, etc.) until you were well rounded in your art. I am pretty sure I checked that box. So, when people call me a building envelope guy, sometimes I respond that I am an architect (only if I am feeling onery). In my world, Architects are supposed to know the building envelope and all the parts and pieces that comprise it. Afterall, architects are the ones that design and seal the envelope. #scary
It took a while for me to understand that technical architects with practical construction experience are not common. When a technical architect is “discovered” word travels faster than a Big Foot sighting; marketing that skill is no longer an issue, the work comes to you. As part of the discovery process (#IYKYK), expert testimony projects come knocking and round about 2010 (maybe earlier) my career expanded to include expert testimony related to the building envelope. All of the building envelope, not just a piece.
Being a technical architect with commercial construction experience, I have always been comfortable with any traditional building system (including stucco) and opining accordingly. However, to be an effective stucco expert, you must establish the street cred of a stucco contractor. Stucco is one of the systems (I would argue roofing is another), where the opinion of an architect or engineer does not match the opinion of a credible (stucco) contractor. The best stucco experts I have ever worked with were not college educated, much less licensed. If I was going to go “toe to toe” with those guys, I needed to up my game. And I did.
In 2017 we teamed up with some of those old school stucco experts, as well as other architects and engineers to build a very large stucco mockup to study what makes stucco crack and whether the cutting of lath behind control joints (required by code referenced standards) really reduced cracking. I have not seen any previous effort that matched the size or intensity of our mockup…and I have looked. Our study concluded that it really did not matter if you cut the lath or not. In fact, the only thing that influenced crack reduction in our study was moist curing. We were not able to get the standard changed, but our effort is still referenced today and my stock as an “expert” went up…few people now had my combined education, training, and experience.
Cracking in stucco remains a hot topic. We currently have over 100 active stucco files (cases) under review where there are claims of damage related to cracks in stucco. That is a lot, especially when you consider that litigation support is less than 10% of what we do. The plaintiffs in many of these cases claim that there is damage related to water infiltration through these cracks. Well, now you really are cracking me up and your expert’s cred as an envelope guy just crashed. If the drainage plane behind the stucco is installed properly (flashed out at windows, etc), then the stucco could be missing altogether, and the building should still not leak. Water that gets behind the stucco should be controlled at the drainage plane (via the WRB) and be directed away from the building via flashings and weeps. Just like God and Chapter 14 of the IBC intended (a 9th day creation). Now, does it always happen that way? No. Would Stucco perform better if we provided a real drainage cavity behind the Stucco? Certainly. Just like every other cladding system, stucco is typically a drainable system, and drainable systems require legitimate drainage.
So why is stucco so feared? Well, it’s because it is not very forgiving, and its success depends on so much more than the performance of the stucco guy. Lightweight sheathing = cracks. Sheathing that is left exposed, gets wet a hundred times during construction, then covered, then AC is energized = cracks. Poor drainage = cracks. If it comes in a sack = cracks. Workmanship can also influence cracking, but with so many other things going on, it can be hard to tell. Sounds terrible until you figure out that it is nothing that basic design and construction sequencing/coordination cannot handle. So why does stucco require more respect than other claddings? Well, we are back to the fact that Stucco is intimate with the sheathing and the installation (by pure nature of the beast) makes Swiss cheese out of the WRB. The WRB selection logic for each project has to consider things like the cladding choice, does it need to breathe (it does if there are two vapor retarders in the same plane…remember some interior finishes, like vinyl wall covering, are vapor retarders), what kind of continuous insulation required (is glued or screwed), fire ratings, and does it need to be self-healing/sealing. This exercise needs to be run with every wall assembly, stucco just does not let you cheat. Also remember WRB’s are not one size fits all.
The moral of this story? It takes more than even a great stucco guy, to produce an even acceptable stucco installation. Decisions made by the project team (that are beyond the stucco guys’ control) will influence the performance of his system. If all architects were created equal (equally technical that is), then wall design would be an easy box to check. But technical architects are not the norm; as it turns out they are the architectural equivalent of Big Foot. The good news is that you can #callmesasquatch.
Till next month.
Images
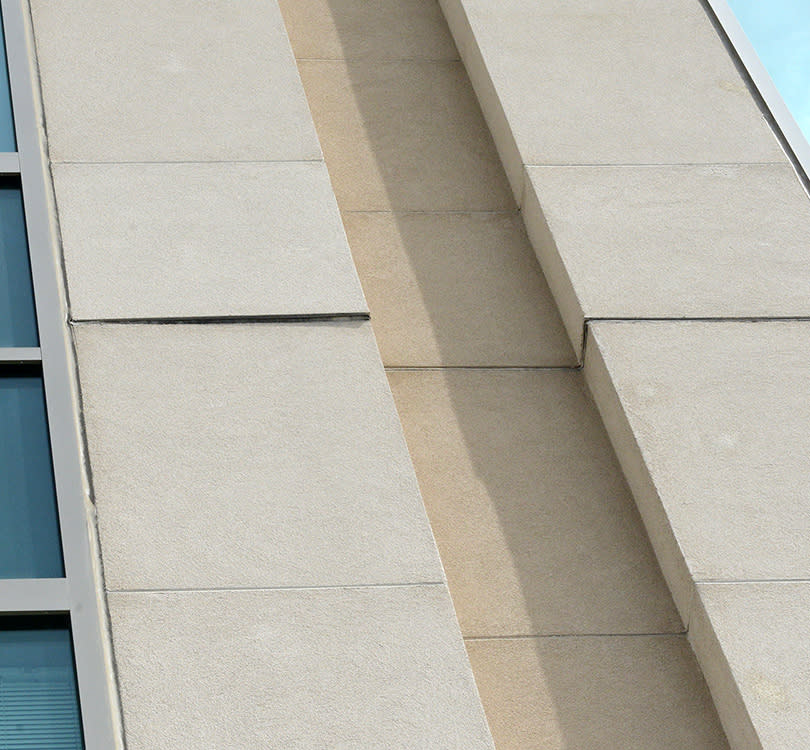
Additional Info
Source : Bill Coltzer, Jr., AIA, BERM